Reduce Interruptions: Maintenance Tips for Coffee Gear Upkeep
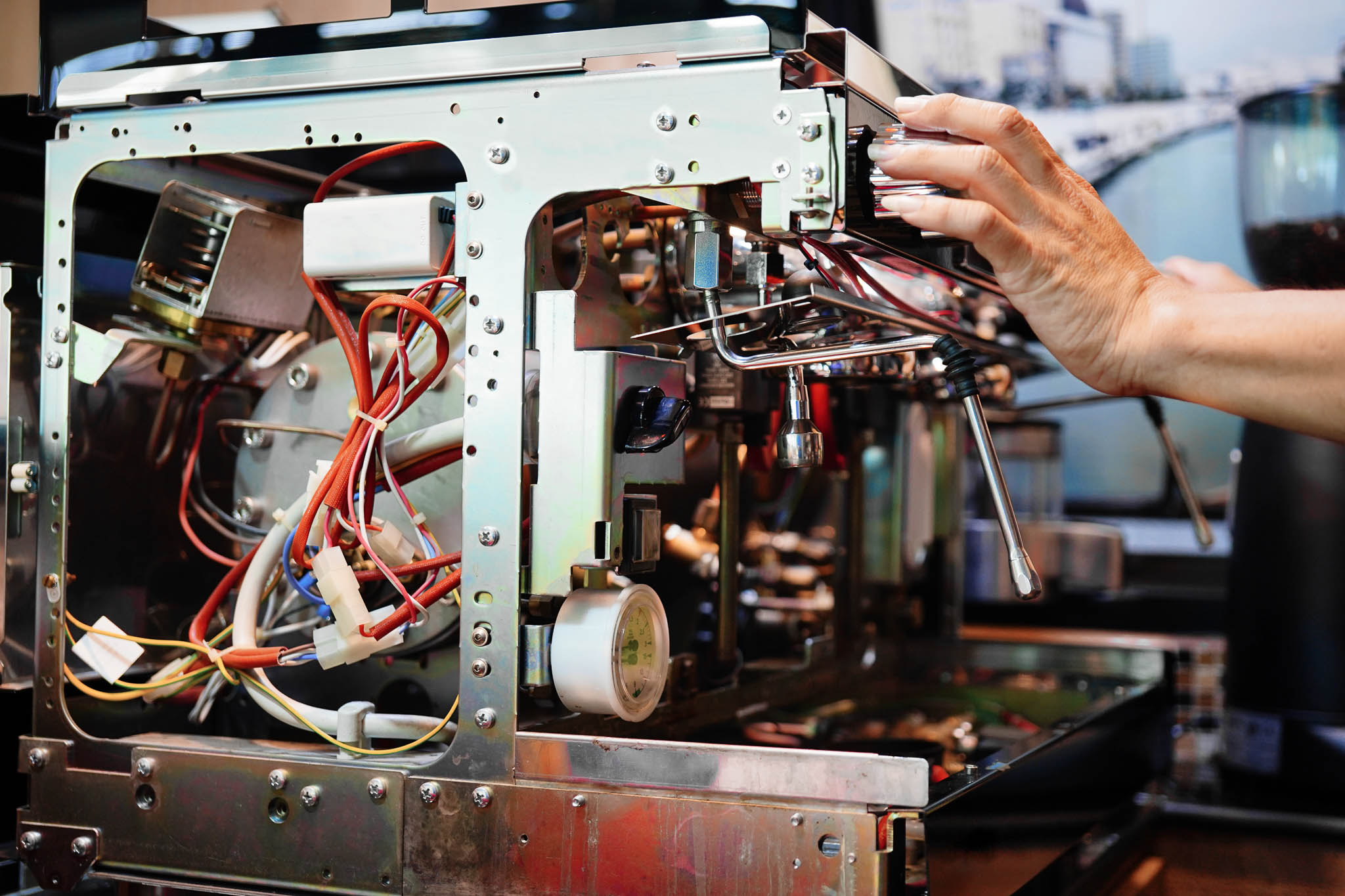
Effective Tactics to Reduce Interruptions: Maintenance Tips for Coffee Gear Upkeep
Ensuring that your coffee brewing operations run without a hitch is paramount, especially when equipment malfunction threatens your business continuity. Downtime can be expensive and harmful to customer satisfaction. However, with thoughtful maintenance strategies and responsive repair services, interruptions can be significantly reduced, allowing you to continue delighting customers with aromatic brews and steamy espressos. Drawing upon the expertise of TheEspressoRPM Company, this article outlines effective tactics to keep your coffee gear in peak condition.
Proactive Maintenance Plans
One of the most reliable ways to minimize downtime is to engage in proactive maintenance of your coffee equipment. Regularly scheduled check-ups can anticipate and prevent many issues before they escalate into full-blown problems that require extensive repair.
- Routine Inspection: A thorough inspection can uncover early signs of wear and tear, allowing for timely interventions.
- Cleaning Regimen: Build-up of coffee oils and mineral deposits can harm equipment; a diligent cleaning protocol is essential.
- Replace Worn Parts: Identifying components that are near the end of their life and replacing them can avert failures.
Having a Reliable Repair Service
When malfunctions occur, having immediate access to skilled technicians is crucial for swift recovery. Expert repair services provided by TheEspressoRPM Company ensure that equipment is fixed promptly to minimize any operational disruption.
- Faster Response Time: Choosing a service that can react quickly and efficiently can reduce the duration of downtime.
- Qualified Technicians: Technicians with specialized coffee equipment expertise ensure a higher quality of repair.
Stocking Essential Spare Parts
One of the causes of extended downtime is the absence of required spare parts. Having a strategic stock of essential parts either on-site or with a nearby service provider can cut short the waiting period involved in sourcing these components.
It's beneficial to consult with service experts about the most commonly needed parts for your specific coffee machines. EspressoRPM's extensive inventory ensures that the right parts are available when you need them.
Implementing an Emergency Plan
Despite best efforts, emergencies can occur. A structured emergency plan will mitigate the impact:
- Determine Critical Equipment: Not every piece of equipment will have an equal effect on operations during downtime. Prioritize your gear accordingly.
- Have a Backup: If possible, keep backup equipment to switch over in the case of a primary machine's failure.
- Train Staff: Ensure your staff are trained to recognize issues early and know the immediate steps to take.
Enhancing Communication
Clear communication channels between your establishment and your service provider are vital. Regular updates on the condition of equipment, swift reporting of issues, and knowledgeable consultations all contribute to reducing repair times. Specialized equipment sales and consultations offered by The EspressoRPM Company, can further streamline the process.
Maintenance, foresight, and efficient communication are the linchpins of minimizing downtime. By partnering with a dedicated service provider and implementing these strategies, you can ensure your coffee gear remains reliable and your business thrives.